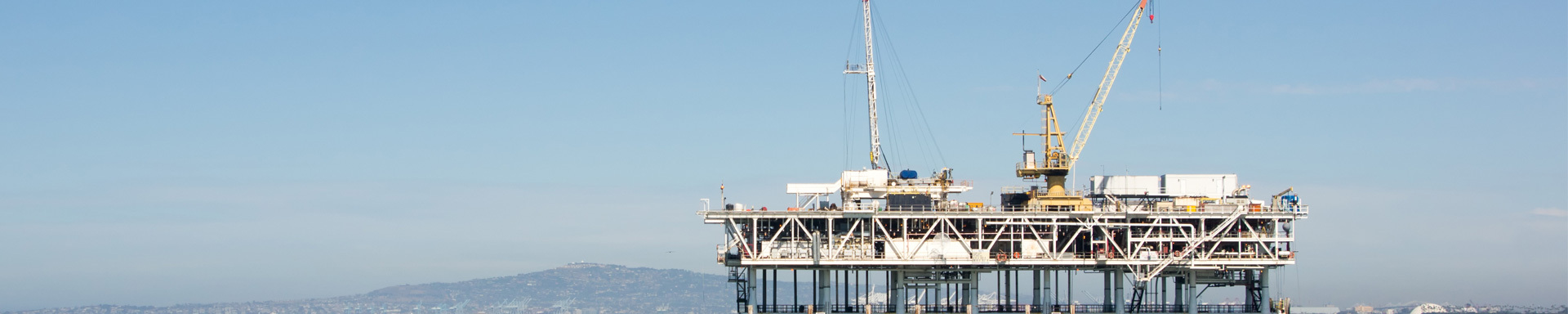
Процесс производства нефтяных бурильных труб разделен на три части.
2024-08-12 10:00Бурильная трубаПроцесс производства нефтяных бурильных труб разделен на три части.
Производство бурильных труб обычно включает в себя три этапа: утолщение конца трубы, обработку замков, сварку трением и последующую обработку.
1. Утолщение конца трубы
Материал корпуса нефтяных бурильных труб – низкоуглеродистая легированная сталь. Круглая стальная заготовка непрерывного литья и прокатки нагревается в большой вращающейся печи, а затем поступает в удлинительную машину и автоматическую прошивную машину для формовки. После повторного нагрева внутренний и внешний диаметры уточняются и выпрямляются, чтобы перейти к процессу ковки. Поскольку сварной шов бурильных труб является самым слабым звеном в процессе использования, перед сваркой бесшовную трубу необходимо утолщать на обоих концах тела трубы, чтобы увеличить толщину и повысить прочность слабых частей, чтобы общая прочность сварной шов превышает общую прочность тела трубы. В зависимости от диаметра труб их обычно делят на три типа: внутреннее и внешнее утолщение, внутреннее утолщение и внешнее утолщение, среди которых основным является тип внутреннего и внешнего утолщения. Процесс утолщения конца трубы заключается в том, чтобы сначала нагреть и выровнять конец бесшовной трубы; во-вторых, конец трубы протыкается гидравлическим или пневматическим способом, внешняя поверхность формируется с помощью формы, а внутренняя поверхность естественным образом формируется за счет температурного градиента; в заключение все тело трубы подвергается термообработке, правке и неразрушающему контролю. Ключевой технологией утолщения концов труб является формирование переходной зоны внутренней поверхности, поскольку эта часть является самой слабой и сложной в эксплуатации, и около 70% аварий происходит именно в этой части, поэтому очень важно качество утолщения концов труб. бурильная труба.
2. Обработка замков
Материалом замков обычно является среднеуглеродистая легированная сталь. Заготовку штампуют трижды после нагрева, а затем обрабатывают после нормализации. Сначала внутреннее отверстие, внешний круг и торцевая поверхность заготовки обтачиваются, а затем соединение закаляется и подвергается термообработке для получения комплексных механических свойств. Наконец, соединение имеет резьбу, а резьбовая часть должна быть покрыта медью или фосфатирована, чтобы предотвратить прилипание во время использования.
Качество соединения зависит от двух ключевых процессов: термообработки и обработки резьбы. Организация термообработки напрямую влияет на механические свойства соединения, поэтому современные заводы по производству бурильных труб используют полностью автоматический непрерывный контролируемый нагрев в атмосфере, закалку закалочным агентом на масляной или водной основе, а также снижение защиты атмосферы в процессе нагрева соединения, чтобы гарантировать, что заготовка не окисленные, обезуглероженные и науглероженные. После закалки и отпуска соединения поочередно проводятся испытания на твердость поверхности и магнитопорошковый контроль. После термообработки проводится обработка резьбы. Резьба бурильной трубы представляет собой коническую резьбу с крупным шагом. В процессе соединения бурильной трубы ключевую роль играет резьба. Таким образом, обработка резьбы в основном выполняется на высокоточных станках с ЧПУ, а расстояние закрытия резьбы, шаг, конусность, высота зуба и другие параметры обрабатываемых соединений измеряются один за другим, чтобы обеспечить тип пряжки резьбы и требования к точности. тем самым эффективно обеспечивая надежность соединения соединения бурильных труб.
3. Сварка трением и последующая обработка.
Сварка трением бурильных труб является важной частью всего производства бурильных труб. Чтобы обеспечить качество сварки, почти все заводы по производству бурильных труб используют полностью автоматические машины для сварки трением и оснащены устройствами контроля параметров сварки для автоматического контроля и записи таких параметров, как время трения, давление трения, давление осадки, время осадки и укорочение во время сварки. , чтобы обеспечить качество сварного шва. После сварки необходимо удалить сварочные заусенцы, закалить зону термического влияния сварки и проверить сварной шов методом неразрушающего контроля. Среди них очень важное значение имеет отпускная термообработка сварного шва. Почти все производители используют среднечастотный нагрев для проведения обработки и автоматически записывают такие параметры, как температура нагрева, время нагрева, время изоляции и время закалки. Преимуществами данной термообработки сварного шва являются: зона термического влияния при нагреве узкая и время нагрева короткое; зона сварного шва имеет равномерную и стабильную структуру и надежную работу; остаточные напряжения на поверхности зоны сварки невелики.